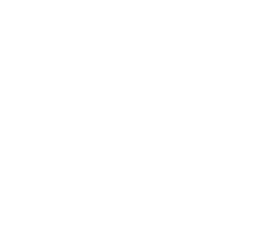
From Bin to Bale:
Recyclables at
Recology Pier 96 MRF

PART 2: Recology and the Blue Bin
The Recology approach to resource recovery is unique and is perhaps best told through the company’s integrated waste systems in San Francisco, California. The three-cart collection system, pioneered by Recology beginning in the 1990s, developed into a comprehensive curbside program that made recycling and organic waste collection available to residents and businesses citywide.
When San Francisco companies and residents place recyclables like single-use plastic in their blue bins, the contents are collected by 180 Recology trucks and deposited at Pier 96’s Recycle Central, the largest material recovery facility (MRF) on the West Coast.
From Bin to Bale:
Recyclables at
Recology Pier 96 MRF
Samples taken from SF blue bins
Samples taken from SF blue bins
Samples taken from SF blue bins
Recology collection trucks arrive at Pier 96 MRF (Material Recovery Facility) and deposit mixed recyclables collected from their routes throughout San Francisco.
From the tipping floor, a loader deposits the mixed recyclables into a hopper, where materials begin their journey through the facility’s expansive sorting system.
From the tipping floor, a loader deposits the mixed recyclables into a hopper, where materials begin their journey through the facility’s expansive sorting system.
From the tipping floor, a loader deposits the mixed recyclables into a hopper, where materials begin their journey through the facility’s expansive sorting system.
At the first stop for mixed recyclables that come off the tipping floor, sorters remove bulky items and large contaminants that might present issues with the spinning machinery, including large film plastics, wires, clothing, wood, and large metal pieces.
At the first stop for mixed recyclables that come off the tipping floor, sorters remove bulky items and large contaminants that might present issues with the spinning machinery, including large film plastics, wires, clothing, wood, and large metal pieces.
At the first stop for mixed recyclables that come off the tipping floor, sorters remove bulky items and large contaminants that might present issues with the spinning machinery, including large film plastics, wires, clothing, wood, and large metal pieces.
After the pre-sort, mixed recyclables encounter a series of spinning “star screens”. Large and light material, notably cardboard, floats above the star screens and is directed onto a conveyor that goes to a baler. Smaller items, including plastic bottles, cans, jars, and paper fall below the star screens onto a separate conveyor for further sorting.
After the pre-sort, mixed recyclables encounter a series of spinning “star screens”. Large and light material, notably cardboard, floats above the star screens and is directed onto a conveyor that goes to a baler. Smaller items, including plastic bottles, cans, jars, and paper fall below the star screens onto a separate conveyor for further sorting.
After the pre-sort, mixed recyclables encounter a series of spinning “star screens”. Large and light material, notably cardboard, floats above the star screens and is directed onto a conveyor that goes to a baler. Smaller items, including plastic bottles, cans, jars, and paper fall below the star screens onto a separate conveyor for further sorting.
Coded as “OCC”, which stands for “Old Corrugated Cardboard”
The smaller material that fell below the star screens now heads through a series of Lubo screens, which are similar in both design and purpose to the previous “star screens”.
The lighter material - mostly paper and plastic items - ride over the screens (like the cardboard did on the previous star screens), while glass, metal, and heavier plastic containers fall down to be further sorted according to their material type.
The smaller material that fell below the star screens now heads through a series of Lubo screens, which are similar in both design and purpose to the previous “star screens”.
The lighter material - mostly paper and plastic items - ride over the screens (like the cardboard did on the previous star screens), while glass, metal, and heavier plastic containers fall down to be further sorted according to their material type.
The smaller material that fell below the star screens now heads through a series of Lubo screens, which are similar in both design and purpose to the previous “star screens”.
The lighter material - mostly paper and plastic items - ride over the screens (like the cardboard did on the previous star screens), while glass, metal, and heavier plastic containers fall down to be further sorted according to their material type.
The lighter materials that rode over the top of the Lubo screens then encounters optical sorters. These state-of-the-art Pellenc (pronounced “puh-lonk) systems use infrared technology to identify plastic containers (bottles, tubs, jars, etc) and uses a puff of air to “shoot” these containers onto a different conveyor so they can be further sorted by plastic type. The paper continues on to the last human sort line before getting baled.
The lighter materials that rode over the top of the Lubo screens then encounters optical sorters. These state-of-the-art Pellenc (pronounced “puh-lonk) systems use infrared technology to identify plastic containers (bottles, tubs, jars, etc) and uses a puff of air to “shoot” these containers onto a different conveyor so they can be further sorted by plastic type. The paper continues on to the last human sort line before getting baled.
The lighter materials that rode over the top of the Lubo screens then encounters optical sorters. These state-of-the-art Pellenc (pronounced “puh-lonk) systems use infrared technology to identify plastic containers (bottles, tubs, jars, etc) and uses a puff of air to “shoot” these containers onto a different conveyor so they can be further sorted by plastic type. The paper continues on to the last human sort line before getting baled.
The paper-rich material that passed the optical sorters passes a final line of human sorters who remove any remaining contaminants (mostly film plastics). After this step, the paper will be compressed into bales and sold to paper recyclers.
The paper-rich material that passed the optical sorters passes a final line of human sorters who remove any remaining contaminants (mostly film plastics). After this step, the paper will be compressed into bales and sold to paper recyclers.
The paper-rich material that passed the optical sorters passes a final line of human sorters who remove any remaining contaminants (mostly film plastics). After this step, the paper will be compressed into bales and sold to paper recyclers.
[left/below] THE CARDBOARD LINE
The material that rode atop the initial star screens, just after the “pre sort”.
[top/middle] THE CONTAINER LINE
Material that fell through the star screens and then fell below again below the Lubo screens. It will be separated by optical and human sorters, magnets, and robots into different resin and metal types.
[right] The “old” paper line, used as overflow during high-volume-processing times. This is the light material that goes over the Lubo screens, but then bypasses the Pellenc optical sorters (they can only handle so much at a time) and instead goes straight to human sorters who remove the remaining film plastics before the material goes into the paper baler.
[left/below] THE CARDBOARD LINE
The material that rode atop the initial star screens, just after the “pre sort”.
[top/middle] THE CONTAINER LINE
Material that fell through the star screens and then fell below again below the Lubo screens. It will be separated by optical and human sorters, magnets, and robots into different resin and metal types.
[right] The “old” paper line, used as overflow during high-volume-processing times. This is the light material that goes over the Lubo screens, but then bypasses the Pellenc optical sorters (they can only handle so much at a time) and instead goes straight to human sorters who remove the remaining film plastics before the material goes into the paper baler.
[left/below] THE CARDBOARD LINE
The material that rode atop the initial star screens, just after the “pre sort”.
[top/middle] THE CONTAINER LINE
Material that fell through the star screens and then fell below again below the Lubo screens. It will be separated by optical and human sorters, magnets, and robots into different resin and metal types.
[right] The “old” paper line, used as overflow during high-volume-processing times. This is the light material that goes over the Lubo screens, but then bypasses the Pellenc optical sorters (they can only handle so much at a time) and instead goes straight to human sorters who remove the remaining film plastics before the material goes into the paper baler.
The plastic bottles, jars, and tubs pass through a final sort, both by human hands and advanced robotics using infrared technology to identify and separate plastics by resin type: typically PET #1, HDPE #2, and Mix #3-7. The sorted plastics then drop into different cages that, upon reaching the appropriate weight, are diverted to the baler where they are compacted into 1,100 to 1,300-pound bricks and staged for sale.
The plastic bottles, jars, and tubs pass through a final sort, both by human hands and advanced robotics using infrared technology to identify and separate plastics by resin type: typically PET #1, HDPE #2, and Mix #3-7. The sorted plastics then drop into different cages that, upon reaching the appropriate weight, are diverted to the baler where they are compacted into 1,100 to 1,300-pound bricks and staged for sale.
The plastic bottles, jars, and tubs pass through a final sort, both by human hands and advanced robotics using infrared technology to identify and separate plastics by resin type: typically PET #1, HDPE #2, and Mix #3-7. The sorted plastics then drop into different cages that, upon reaching the appropriate weight, are diverted to the baler where they are compacted into 1,100 to 1,300-pound bricks and staged for sale.
Rigid plastic containers collected by the robots end in this 40 cubic yard box. For reference, a standard dumpster you see behind a restaurant or apartment building is generally between 2 and 6 cubic yards. This plastic will be baled and sold for recycling.
Rigid plastic containers collected by the robots end in this 40 cubic yard box. For reference, a standard dumpster you see behind a restaurant or apartment building is generally between 2 and 6 cubic yards. This plastic will be baled and sold for recycling.
Rigid plastic containers collected by the robots end in this 40 cubic yard box. For reference, a standard dumpster you see behind a restaurant or apartment building is generally between 2 and 6 cubic yards. This plastic will be baled and sold for recycling.
Loader holding a bucket-full of PET #1 plastics, preparing to be baled and staged for sale.
Loader holding a bucket-full of PET #1 plastics, preparing to be baled and staged for sale.
Loader holding a bucket-full of PET #1 plastics, preparing to be baled and staged for sale.
Loader dumping PET #1 plastics onto a conveyor belt that leads to the baler.
Loader dumping PET #1 plastics onto a conveyor belt that leads to the baler.
Loader dumping PET #1 plastics onto a conveyor belt that leads to the baler.
A finished cardboard bale followed by finished plastic (PET #1) bale. The same baler is used throughout the day for multiple material types, including paper, cardboard, and various metal and plastic types.
Baled plastics are shipped to domestic and international recyclers who shred, clean, melt, and pelletize the materials, which will in turn be sold to manufacturers to use in products like carpet, clothing, insulation, automotive parts, plastic lumber, and new bottles and containers. While most high-grade resins, such as PET #1 and HDPE #2 are sold to domestic recyclers, most lower-grade resins, such as #3-7, are shipped to overseas markets, predominantly in southeast Asia.
A finished cardboard bale followed by finished plastic (PET #1) bale. The same baler is used throughout the day for multiple material types, including paper, cardboard, and various metal and plastic types.
Baled plastics are shipped to domestic and international recyclers who shred, clean, melt, and pelletize the materials, which will in turn be sold to manufacturers to use in products like carpet, clothing, insulation, automotive parts, plastic lumber, and new bottles and containers. While most high-grade resins, such as PET #1 and HDPE #2 are sold to domestic recyclers, most lower-grade resins, such as #3-7, are shipped to overseas markets, predominantly in southeast Asia.
A finished cardboard bale followed by finished plastic (PET #1) bale. The same baler is used throughout the day for multiple material types, including paper, cardboard, and various metal and plastic types.
Baled plastics are shipped to domestic and international recyclers who shred, clean, melt, and pelletize the materials, which will in turn be sold to manufacturers to use in products like carpet, clothing, insulation, automotive parts, plastic lumber, and new bottles and containers. While most high-grade resins, such as PET #1 and HDPE #2 are sold to domestic recyclers, most lower-grade resins, such as #3-7, are shipped to overseas markets, predominantly in southeast Asia.
The Baler
The Baler
THE BALER
Baled mixed plastics are a combination of small to medium sized #3 - #7 resins. These are lesser-valued commodities, as they are lower-quality resins and must be further separated by recyclers.
Baled mixed plastics are a combination of small to medium sized #3 - #7 resins. These are lesser-valued commodities, as they are lower-quality resins and must be further separated by recyclers.
Baled mixed plastics are a combination of small to medium sized #3 - #7 resins. These are lesser-valued commodities, as they are lower-quality resins and must be further separated by recyclers.
Baled milk jugs and other HDPE #2 plastics are currently the highest-valued plastic commodity, though prices fluctuate regularly. In addition to being recycled into new HDPE containers, a common product made from recycled HDPE is plastic lumber, used in decks, boardwalks, and benches.
Baled milk jugs and other HDPE #2 plastics are currently the highest-valued plastic commodity, though prices fluctuate regularly. In addition to being recycled into new HDPE containers, a common product made from recycled HDPE is plastic lumber, used in decks, boardwalks, and benches.
Baled milk jugs and other HDPE #2 plastics are currently the highest-valued plastic commodity, though prices fluctuate regularly. In addition to being recycled into new HDPE containers, a common product made from recycled HDPE is plastic lumber, used in decks, boardwalks, and benches.
Green and brown glass, dropped off by public “buyback” customers - part of the California CRV program. These arrive sorted by color and are mostly “whole” because they did not travel through the facility's conveyor systems.
Green and brown glass, dropped off by public “buyback” customers - part of the California CRV program. These arrive sorted by color and are mostly “whole” because they did not travel through the facility's conveyor systems.
Green and brown glass, dropped off by public “buyback” customers - part of the California CRV program. These arrive sorted by color and are mostly “whole” because they did not travel through the facility's conveyor systems.
Crushed glass is heavy and effectively the last thing that comes off the MRF line.
Crushed glass is heavy and effectively the last thing that comes off the MRF line.
Crushed glass is heavy and effectively the last thing that comes off the MRF line.
Residual Fines
Residual Fines
RESIDUAL FINES
Not everything that arrives at recycling facilities can get recovered, even at facilities as advanced as Pier 96. Handling 650+ tons of material per day means some small pieces still manage to make it through the entire process without being captured.
Not everything that arrives at recycling facilities can get recovered, even at facilities as advanced as Pier 96. Handling 650+ tons of material per day means some small pieces still manage to make it through the entire process without being captured.
Not everything that arrives at recycling facilities can get recovered, even at facilities as advanced as Pier 96. Handling 650+ tons of material per day means some small pieces still manage to make it through the entire process without being captured.
MRFs sort these mixed recyclables into distinct commodities and prepare them for sale. This preparation includes sorting plastics by resin type, and paper, metals, and glass by different grades, colors, and quality. By the time these materials work their way through the facility’s sorting systems, close to 90% of the materials that arrive will be recovered and sold for recycling.
All plastics are not created equal. While proven and often domestic recycling solutions exist for high-grade resins, manufacturers continue to engineer newer, cheaper, and disposable products with distinct chemical properties that enhance flexibility, appearance, and convenience. For much of this new generation of plastics, the economics of recovery and thus scalable recycling solutions do not yet exist.
MATERIAL RECOVERY FACILITY (MRF). After a customer puts their recyclables in a bin, they are collected and brought to a MRF, where they are sorted and baled by material type. To maximize the recovery of plastics, a MRF usually ships different materials to specialized processing facilities where they are cleaned, shredded, and pelletized to become “raw” materials that can be re-incorporated into the manufacturing of new products. While metals, paper, and glass have clearly defined recycling streams, plastics are made from a variety of resins, which are often combined, making their recovery a costly and complex process. Most higher-grade (#1-2) plastics are sold to domestic recyclers, while #3-7 mixed are shipped to Asia. While plastics manufacturers constantly make cheaper, lighter resins with distinct qualities (rigidity, flexibility, durability, etc.) and therefore different chemical properties, these new plastics will, in turn, require new recycling methods. These evolving plastics require new and different processing methods, and in many cases, they are designed for disposability instead of recovery.
It is important to consider that while recycling plastics is a better alternative to incineration or landfilling, it’s a misconception to think that plastic, even when recycled, has no environmental impact. Collecting, processing, transporting, and recycling plastics uses energy, fuel, and water. Most plastics that are recycled are actually downcycled, meaning their transformation into products like plastic lumber, fiberglass, or clothing breaks the closed-loop system. While these products are manufactured from recycled plastics, they have little to no likelihood of being recycled again once their utility has expired. In these cases, recycling is only a partial solution. Plastic producers, consumers, and resource recovery providers must continue working together to create a true closed-loop system that does not result in landfilled or downcycled products.
California’s state-funded deposit program, known as the California Redemption Value (CRV), might not be broken – but it is becoming obsolete.
In 1986, in an effort to spark recycling participation, the California legislature enacted the Bottle Bill or AB 2020, formally known as the Beverage Container Recycling and Litter Reduction Act. Through this program, beverage manufacturers and distributors are charged a deposit that is passed on to retailers and ultimately to individual consumers. This deposit, typically 5 or 10 cents per container, can be redeemed when the consumer returns the CRV-eligible container to a certified recycling center. Program fees, when combined with statewide unredeemed funds, help fund city and county recycling programs, recycling market development, grants to nonprofits and conservation agencies, and consumer education campaigns.
CALIFORNIA REDEMPTION VALUE (CRV). The California CRV program might not be broken – but it is becoming obsolete. In the past four years, more than 40% of statewide redemption centers have closed. The emergence of curbside recycling programs has become a tenet of California’s progressive waste recovery infrastructure, bringing convenient recycling services to the doorstep of virtually every household, apartment, and business in the state. As such, the need for a deposit-based redemption program has dwindled. Revenues generated from manufacturers may be better spent on market development, education programs, and further support for curbside programs.
While the Bottle Bill was an important catalyst to initiate consumer-level recycling in California, the program is becoming obsolete. The Bill predated the emergence of curbside recycling programs – like those offered by Recology – in California. Today, the widespread availability of recycling programs has become a core tenet of California’s progressive waste recovery infrastructure, as Recology and other service providers deliver convenient recycling services to the doorstep of virtually every household, apartment, and business in the state. As such, the need for a deposit-based redemption program has dwindled.
Limitations of the bill’s scope and flexibility have created additional barriers to its widespread success. As it is limited to only certain qualifying single-use beverage containers, the program covers less than 4% of the waste stream. What’s more, the redemption value paid back to recycling centers (to cover the cost of what they pay consumers who redeem their CRV recyclables) does not cover increasing processing costs nor make up for sharply lower commodity prices. As a result, between 2015 and 2019, more than 1,000 CRV redemption centers, about 40% of locations statewide, closed.
Recycling centers that participate in the California CRV program, like the Recology-operated facility above in San Francisco, are in increasingly short supply. Since 2015, some 40% of statewide centers have closed amid elevated operating costs, dwindling commodity prices, and public pressure.
Most recently, in August 2019, RePlanet, the largest remaining independent provider of CRV-redemption centers, shuttered its remaining 280 locations and laid off its entire 750-person workforce. Clearly, the CRV program – while an important step to initiate consumer-level recycling in California – is becoming a relic of a bygone era.
About
The Single-Use Plastics Platform is produced by The Lexicon, an international NGO that brings together food companies, government agencies, financial institutions, scientists, entrepreneurs, and food producers from across the globe to tackle some of the most complex challenges facing our food systems.
Team
The Single-Use Plastics Platform was developed by Green Brown Blue, an invitation-only food systems solutions activator produced by The Lexicon with support from Food at Google. The activator model fosters unprecedented collaborations between leading food service companies, environmental NGOs, government agencies, and technical experts from across the globe.
This website was built by The Lexicon™, a 501(c)(3) tax-exempt nonprofit organization headquartered in Petaluma, CA.
Check out our Privacy Policy, Cookie Policy, and Terms of Use.
© 2024 – Lexicon of Food™
Professionals at universities and research institutions seeking scholarly articles, data, and resources.
Tools to align investment and grant making strategies with advances in agriculture, food production, and emerging markets.
Professionals seeking information on ingredient sourcing, menu planning, sustainability, and industry trends.
Chefs and food industry professionals seeking inspiration on ingredients and sustainable trends to enhance their work.
Individuals interested in food products, recipes, nutrition, and health-related information for personal or family use.
Individuals producing food, fiber, feed, and other agricultural products that support both local and global food systems.
This online platform is years in the making, featuring the contributions of 1000+ companies and NGOs across a dzen domain areas. To introduce you to their work, we’ve assembled personalized experiences with insights from our community of international experts.
Businesses engaged in food production, processing, and distribution that seek insight from domain experts
Those offering specialized resources and support and guidance in agriculture, food production, and nutrition.
Individuals who engage and educate audience on themes related to agriculture, food production, and nutrition.
Nutritional information for professionals offering informed dietary choices that help others reach their health objectives
Those advocating for greater awareness and stronger action to address climate impacts on agriculture and food security.
Professionals seeking curriculum materials, lesson plans, and learning tools related to food and agriculture.
We have no idea who grows our food, what farming practices they use, the communities they support, or what processing it undergoes before reaching our plates.
As a result, we have no ability to make food purchases that align with our values as individuals, or our missions as companies.
To change that, we’ve asked experts to demystify the complexity of food purchasing so that you can better informed decisions about what you buy.
The Lexicon of Food’s community of experts share their insights and experiences on the complex journey food takes to reach our plates. Their work underscores the need for greater transparency and better informed decision-making in shaping a healthier and more sustainable food system for all.
Over half the world’s agricultural production comes from only three crops. Can we bring greater diversity to our plates?
In the US, four companies control nearly 85% of the beef we consume. Can we develop more regionally-based markets?
How can we develop alternatives to single-use plastics that are more sustainable and environmentally friendly?
Could changing the way we grow our food provide benefits for people and the planet, and even respond to climate change?
Can we meet the growing global demand for protein while reducing our reliance on traditional animal agriculture?
It’s not only important what we eat but what our food comes in. Can we develop tools that identify toxic materials used in food packaging?
Explore The Lexicon’s collection of immersive storytelling experiences featuring insights from our community of international experts.
The Great Protein Shift
Our experts use an engaging interactive approach to break down the technologies used to create these novel proteins.
Ten Principles for Regenerative Agriculture
What is regenerative agriculture? We’ve developed a framework to explain the principles, practices, ecological benefits and language of regenerative agriculture, then connected them to the UN’s Sustainable Development Goals.
Food-related chronic diseases are the biggest burden on healthcare systems. What would happen if we treated food as medicine?
How can we responsibly manage our ocean fisheries so there’s enough seafood for everyone now and for generations to come?
Mobilizing agronomists, farmers, NGOs, chefs, and food companies in defense of biodiversity in nature, agriculture, and on our plates.
Can governments develop guidelines that shift consumer diets, promote balanced nutrition and reduce the risk of chronic disease?
Will sustainably raising shellfish, finfish, shrimp and algae meet the growing demand for seafood while reducing pressure on wild fisheries?
How can a universal visual language to describe our food systems bridge cultural barriers and increase consumer literacy?
What if making the right food choices could be an effective tool for addressing a range of global challenges?
Let’s start with climate change. While it presents our planet with existential challenges, biodiversity loss, desertification, and water scarcity should be of equal concern—they’re all connected.
Instead of seeking singular solutions, we must develop a holistic approach, one that channel our collective energies and achieve positive impacts where they matter most.
To maximize our collective impact, EBF can help consumers focus on six equally important ecological benefits: air, water, soil, biodiversity, equity, and carbon.
We’ve gathered domain experts from over 1,000 companies and organizations working at the intersection of food, agriculture, conservation, and climate change.
The Lexicon™ is a California-based nonprofit founded in 2009 with a focus on positive solutions for a more sustainable planet.
For the past five years, it has developed an “activator for good ideas” with support from Food at Google. This model gathers domain experts from over 1,000 companies and organizations working at the intersection of food, agriculture, conservation, and climate change.
Together, the community has reached consensus on strategies that respond to challenges across multiple domain areas, including biodiversity, regenerative agriculture, food packaging, aquaculture, and the missing middle in supply chains for meat.
Lexicon of Food is the first public release of that work.
Over half the world’s agricultural production comes from only three crops. Can we bring greater diversity to our plates?
In the US, four companies control nearly 85% of the beef we consume. Can we develop more regionally-based markets?
How can we develop alternatives to single-use plastics that are more sustainable and environmentally friendly?
Could changing the way we grow our food provide benefits for people and the planet, and even respond to climate change?
Can we meet the growing global demand for protein while reducing our reliance on traditional animal agriculture?
It’s not only important what we eat but what our food comes in. Can we develop tools that identify toxic materials used in food packaging?
Explore The Lexicon’s collection of immersive storytelling experiences featuring insights from our community of international experts.
The Great Protein Shift
Our experts use an engaging interactive approach to break down the technologies used to create these novel proteins.
Ten Principles for Regenerative Agriculture
What is regenerative agriculture? We’ve developed a framework to explain the principles, practices, ecological benefits and language of regenerative agriculture, then connected them to the UN’s Sustainable Development Goals.
Food-related chronic diseases are the biggest burden on healthcare systems. What would happen if we treated food as medicine?
How can we responsibly manage our ocean fisheries so there’s enough seafood for everyone now and for generations to come?
Mobilizing agronomists, farmers, NGOs, chefs, and food companies in defense of biodiversity in nature, agriculture, and on our plates.
Can governments develop guidelines that shift consumer diets, promote balanced nutrition and reduce the risk of chronic disease?
Will sustainably raising shellfish, finfish, shrimp and algae meet the growing demand for seafood while reducing pressure on wild fisheries?
How can a universal visual language to describe our food systems bridge cultural barriers and increase consumer literacy?
This game was designed to raise awareness about the impacts our food choices have on our own health, but also the environment, climate change and the cultures in which we live.
First, you can choose one of the four global regions and pick a character that you want to play.
Each region has distinct cultural, economic, historical, and agricultural capacities to feed itself, and each character faces different challenges, such as varied access to food, higher or lower family income, and food literacy.
As you take your character through their day, select the choices you think they might make given their situation.
At the end of the day you will get a report on the impact of your food choices on five areas: health, healthcare, climate, environment and culture. Take some time to read through them. Now go back and try again. Can you make improvements in all five areas? Did one area score higher, but another score lower?
FOOD CHOICES FOR A HEALTHY PLANET will help you better understand how all these regions and characters’ particularities can influence our food choices, and how our food choices can impact our personal health, national healthcare, environment, climate, and culture. Let’s Play!
The FOOD CHOICES FOR A HEALTHY PLANET game allows users to experience the dramatic connections between food and climate in a unique and engaging way. The venue and the game set-up provides attendees with a fun experience, with a potential to add a new layer of storytelling about this topic.
Starting the game: the pilot version of the game features four country/regions: Each reflects a different way people (and the national dietary guidelines) look at diets: Nordic Countries (sustainability), Brazil (local and whole foods instead of ultra-processed foods); Canada (plant-forward), and Indonesia (developing countries).
Personalizing the game: players begin by choosing a country and then a character who they help in making food choices over the course of one day. Later versions may allow for creating custom avatars.
Making tough food choices: This interactive game for all ages shows how the food choices we make impact our health and the environment, and even contribute to climate change.
What we eat matters: at the end of each game, players learn that every decision they make impacts not only their health, but a national healthcare system, the environment, climate and even culture.
We’d love to know more about you and why you think you will be a great fit for this position! Shoot us an email introducing you and we’ll get back to you as soon as possible!
Providing best water quality conditions to ensure optimal living condition for growth, breeding and other physiological needs
Water quality is sourced from natural seawater with dependency on the tidal system. Water is treated to adjust pH and alkalinity before stocking.
Producers that own and manages the farm operating under small-scale farming model with limited input, investment which leads to low to medium production yield
All 1,149 of our farmers in both regencies are smallholder farmers who operate with low stocking density, traditional ponds, and no use of any other intensification technology.
Safe working conditions — cleanliness, lighting, equipment, paid overtime, hazard safety, etc. — happen when businesses conduct workplace safety audits and invest in the wellbeing of their employees
Company ensure implementation of safe working conditions by applying representative of workers to health and safety and conduct regular health and safety training. The practices are proven by ASIC standards’ implementation
Implementation of farming operations, management and trading that impact positively to community wellbeing and sustainable better way of living
The company works with local stakeholders and local governments to create support for farmers and the farming community in increasing resilience. Our farming community is empowered by local stakeholders continuously to maintain a long generation of farmers.
Freezing seafood rapidly when it is at peak freshness to ensure a higher quality and longer lasting product
Our harvests are immediately frozen with ice flakes in layers in cool boxes. Boxes are equipped with paper records and coding for traceability. We ensure that our harvests are processed with the utmost care at <-18 degrees Celsius.
Sourcing plant based ingredients, like soy, from producers that do not destroy forests to increase their growing area and produce fish feed ingredients
With adjacent locations to mangroves and coastal areas, our farmers and company are committed to no deforestation at any scale. Mangrove rehabilitation and replantation are conducted every year in collaboration with local authorities. Our farms are not established in protected habitats and have not resulted from deforestation activity since the beginning of our establishment.
Implement only natural feeds grown in water for aquatic animal’s feed without use of commercial feed
Our black tiger shrimps are not fed using commercial feed. The system is zero input and depends fully on natural feed grown in the pond. Our farmers use organic fertilizer and probiotics to enhance the water quality.
Enhance biodiversity through integration of nature conservation and food production without negative impact to surrounding ecosysytem
As our practices are natural, organic, and zero input, farms coexist with surrounding biodiversity which increases the volume of polyculture and mangrove coverage area. Farmers’ groups, along with the company, conduct regular benthic assessments, river cleaning, and mangrove planting.
THE TERM “MOONSHOT” IS OFTEN USED TO DESCRIBE an initiative that goes beyond the confines of the present by transforming our greatest aspirations into reality, but the story of a moonshot isn’t that of a single rocket. In fact, the Apollo program that put Neil Armstrong on the moon was actually preceded by the Gemini program, which in a two-year span rapidly put ten rockets into space. This “accelerated” process — with a new mission nearly every 2-3 months — allowed NASA to rapidly iterate, validate their findings and learn from their mistakes. Telemetry. Propulsion. Re-entry. Each mission helped NASA build and test a new piece of the puzzle.
The program also had its fair share of creative challenges, especially at the outset, as the urgency of the task at hand required that the roadmap for getting to the moon be written in parallel with the rapid pace of Gemini missions. Through it all, the NASA teams never lost sight of their ultimate goal, and the teams finally aligned on their shared responsibilities. Within three years of Gemini’s conclusion, a man did walk on the moon.
FACT is a food systems solutions activator that assesses the current food landscape, engages with key influencers, identifies trends, surveys innovative work and creates greater visibility for ideas and practices with the potential to shift key food and agricultural paradigms.
Each activator focuses on a single moonshot; instead of producing white papers, policy briefs or peer-reviewed articles, these teams design and implement blueprints for action. At the end of each activator, their work is released to the public and open-sourced.
As with any rapid iteration process, many of our activators re-assess their initial plans and pivot to address new challenges along the way. Still, one thing has remained constant: their conviction that by working together and pooling their knowledge and resources, they can create a multiplier effect to more rapidly activate change.
Co-Founder
THE LEXICON
Vice President
Global Workplace Programs
GOOGLE
Who can enter and how selections are made.
A Greener Blue is a global call to action that is open to individuals and teams from all over the world. Below is a non-exhaustive list of subjects the initiative targets.
To apply, prospective participants will need to fill out the form on the website, by filling out each part of it. Applications left incomplete or containing information that is not complete enough will receive a low score and have less chance of being admitted to the storytelling lab.
Nonprofit organizations, communities of fishers and fish farmers and companies that are seeking a closer partnership or special support can also apply by contacting hello@thelexicon.org and interacting with the members of our team.
Special attention will be given to the section of the form regarding the stories that the applicants want to tell and the reasons for participating. All proposals for stories regarding small-scale or artisanal fishers or aquaculturists, communities of artisanal fishers or aquaculturists, and workers in different steps of the seafood value chain will be considered.
Stories should show the important role that these figures play in building a more sustainable seafood system. To help with this narrative, the initiative has identified 10 principles that define a more sustainable seafood system. These can be viewed on the initiative’s website and they state:
Seafood is sustainable when:
Proposed stories should show one or more of these principles in practice.
Applications are open from the 28th of June to the 15th of August 2022. There will be 50 selected applicants who will be granted access to The Lexicon’s Total Storytelling Lab. These 50 applicants will be asked to accept and sign a learning agreement and acceptance of participation document with which they agree to respect The Lexicon’s code of conduct.
The first part of the lab will take place online between August the 22nd and August the 26th and focus on training participants on the foundation of storytelling, supporting them to create a production plan, and aligning all of them around a shared vision.
Based on their motivation, quality of the story, geography, and participation in the online Lab, a selected group of participants will be gifted a GoPro camera offered to the program by GoPro For A Change. Participants who are selected to receive the GoPro camera will need to sign an acceptance and usage agreement.
The second part of the Storytelling Lab will consist of a production period in which each participant will be supported in the production of their own story. This period goes from August 26th to October 13th. Each participant will have the opportunity to access special mentorship from an international network of storytellers and seafood experts who will help them build their story. The Lexicon also provides editors, animators, and graphic designers to support participants with more technical skills.
The final deadline to submit the stories is the 14th of October. Participants will be able to both submit complete edited stories, or footage accompanied by a storyboard to be assembled by The Lexicon’s team.
All applicants who will exhibit conduct and behavior that is contrary to The Lexicon’s code of conduct will be automatically disqualified. This includes applicants proposing stories that openly discriminate against a social or ethnic group, advocate for a political group, incite violence against any group, or incite to commit crimes of any kind.
All submissions must be the entrant’s original work. Submissions must not infringe upon the trademark, copyright, moral rights, intellectual rights, or rights of privacy of any entity or person.
Participants will retain the copyrights to their work while also granting access to The Lexicon and the other partners of the initiative to share their contributions as part of A Greener Blue Global Storytelling Initiative.
If a potential selected applicant cannot be reached by the team of the Initiative within three (3) working days, using the contact information provided at the time of entry, or if the communication is returned as undeliverable, that potential participant shall forfeit.
Selected applicants will be granted access to an advanced Storytelling Lab taught and facilitated by Douglas Gayeton, award-winning storyteller and information architect, co-founder of The Lexicon. In this course, participants will learn new techniques that will improve their storytelling skills and be able to better communicate their work with a global audience. This skill includes (but is not limited to) how to build a production plan for a documentary, how to find and interact with subjects, and how to shoot a short documentary.
Twenty of the participants will receive a GoPro Hero 11 Digital Video and Audio Cameras by September 15, 2022. Additional participants may receive GoPro Digital Video and Audio Cameras to be announced at a later date. The recipients will be selected by advisors to the program and will be based on selection criteria (see below) on proposals by Storytelling Lab participants. The selections will keep in accordance with Lab criteria concerning geography, active participation in the Storytelling Lab and commitment to the creation of a story for the Initiative, a GoPro Camera to use to complete the storytelling lab and document their story. These recipients will be asked to sign an acceptance letter with terms of use and condition to receive the camera.
The Lexicon provides video editors, graphic designers, and animators to support the participants to complete their stories.
The submitted stories will be showcased during international and local events, starting from the closing event of the International Year of Fisheries and Aquaculture 2022 in Rome, in January 2023. The authors of the stories will be credited and may be invited to join.
Storytelling lab participation:
Applicants that will be granted access to the storytelling Lab will be evaluated based on the entries they provided in the online form, and in particular:
Applications will be evaluated by a team of 4 judges from The Lexicon, GSSI and the team of IYAFA (Selection committee).
When selecting applications, the call promoters may request additional documentation or interviews both for the purpose of verifying compliance with eligibility requirements and to facilitate proposal evaluation.
Camera recipients:
Participants to the Storytelling Lab who will be given a GoPro camera will be selected based on:
The evaluation will be carried out by a team of 4 judges from The Lexicon, GSSI and the team of IYAFA (Selection committee).
Incidental expenses and all other costs and expenses which are not specifically listed in these Official Rules but which may be associated with the acceptance, receipt and use of the Storytelling Lab and the camera are solely the responsibility of the respective participants and are not covered by The Lexicon or any of the A Greener Blue partners.
All participants who receive a Camera are required to sign an agreement allowing GoPro for a Cause, The Lexicon and GSSI to utilize the films for A Greener Blue and their promotional purposes. All participants will be required to an agreement to upload their footage into the shared drive of The Lexicon and make the stories, films and images available for The Lexicon and the promoting partners of A Greener Blue.